Radiant Tube Inserts (RTIs)
Positively impact emissions, productivity, and quality of industrial radiant tube furnaces with our patented technology.
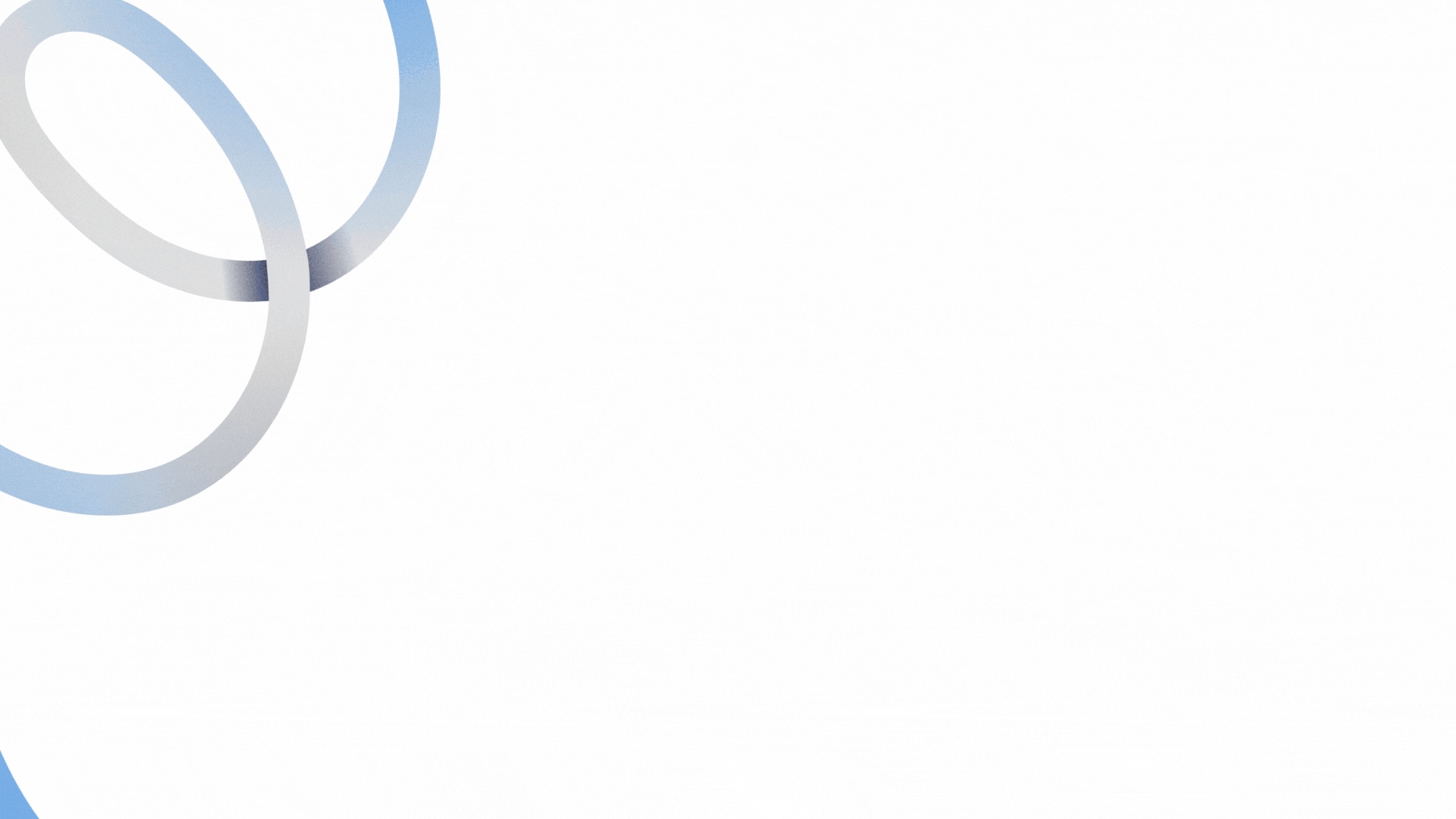
Why Choose PSNERGY's RTI?
Efficiency Improvement. Our patented RTIs can increase furnace efficiency by up to 20%, meet environmental regulations, and consistently deliver high-quality products.
- Increase throughput
- Increase radiant tube life and maximize heat transfer
- Minimize hot spots
- Minimize cracked tubes
- Reduce energy consumption
- Reduce emissions per ton, including NOx & CO
- Redirect wasted energy back to the load
.png?width=500&height=500&name=rti%20(1).png)
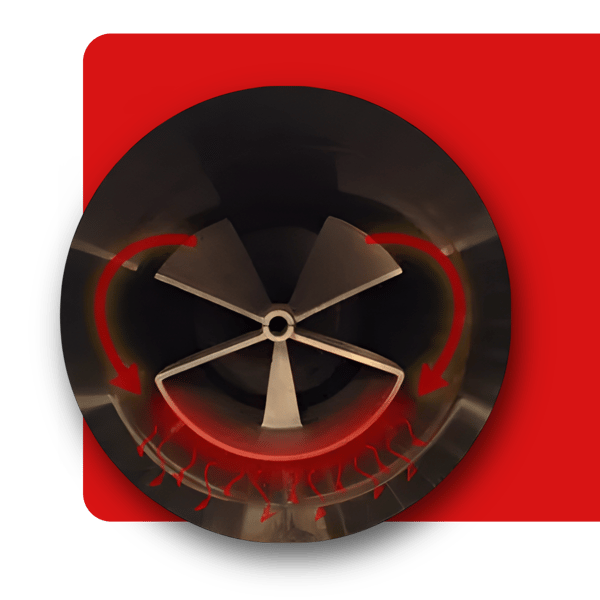
Compatibility.
RTIs can be used in a variety of furnace configurations:
- U-Tubes
- W-Tubes
- Straight Tubes
- Trident Tubes
- Recuperated & Non-recuperated systems
Benefits of Radiant Tube Inserts
NO MATTER THE AGE, SIZE, OR CONDITION OF YOUR FURNACE, OUR RTI'S PROVIDE NUMEROUS BENEFITS
How the RTI Works. Our patented design consists of convective wings that continually mix exhaust flow and drive energy toward the shell. When positioned parallel to the tube surface, the shell maximizes energy transfer toward the load. Composed of silicon carbide, RTIs have near-perfect emissivity, are thermally stable above 3,000 degrees F, and are highly resistant to oxidation.
- Improved Productivity. Increase production rates or reduce gas consumption.
- Improved Quality. Achieve consistent heating and higher product quality.
- Reduced Operating Costs. Save on fuel and maintenance costs.
By increasing the amount of heat energy available in the exhaust leg of the tube and decreasing wasted energy, you can increase your production output per MBTU of natural gas while reducing emissions. Improved productivity can be seen in one of two ways:
- Increased Production. Providing more energy to the load allows for increased line speeds (continuous furnace) or reduced heat-up cycle times (batch furnace) while consuming the same amount of fuel.
- Reduced Emissions with Fuel Savings. Providing more energy to the load while maintaining the same rate of production results in less gas consumption.
Before and After
Figure 1 shows a lack of heat transfer between the inside wall of a radiant tube and hot flue gas flow, resulting in major energy loss out of the stack.

Figure 1. Radiant tube exhaust without PNSERGY inserts.
Figure 2 shows a radiant tube exhaust leg with PSNERGY inserts. Our patented RTI design increases convective and radiant heat transfer within your radiant tubes, decreasing wasted energy and directing that energy to the load.

Figure 2: Radiant tube exhaust leg with PSNERGY inserts.
Simple Solution to Combustion Challenges
Significant energy loss out of the stack, short radiant tube life, high emissions, and slow heat-up time are common combustion challenges. With a quick and efficient installation, our RTIs offer a simple solution to:
- Increase Productivity
- Quick and Easy Installation. Captures and redirects wasted energy without blocking airflow.
- Reduce Heat-Up Time. Improve zone temperature uniformity.
- Works with or without recuperators.
- Patented Design
- Silicon Carbide Composition. 98% emissivity and optimal radiation performance.
- Open Cross Section. Absorbs exhaust gas heat and radiates energy into the load without back pressure on the burner.
- Reduce Emissions
- Decreases Overall Emissions. Including NOx and CO.
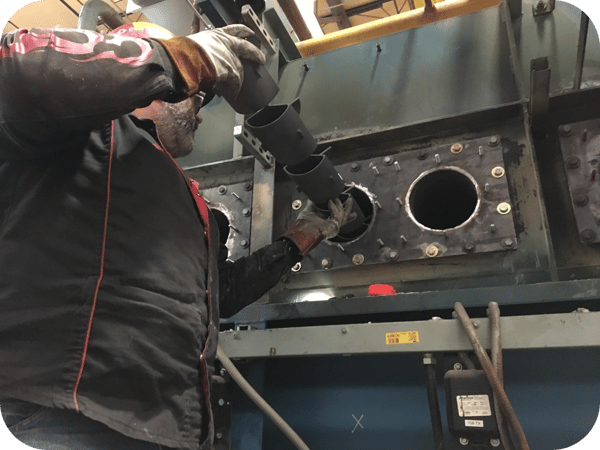
Patent Number: US010823396B2
Patent Number: US1003086782